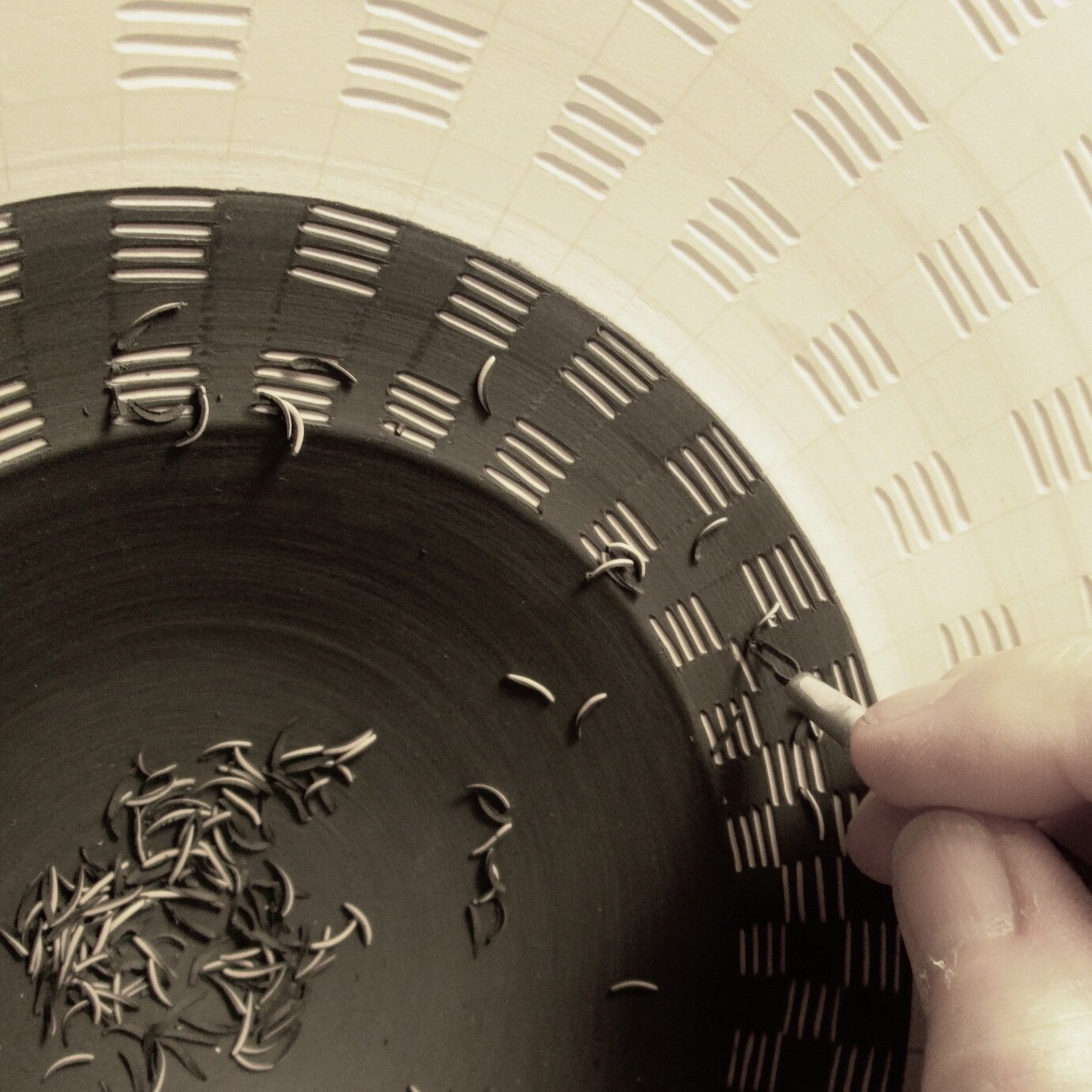
My Process
All of my pieces are one of a kind, formed on my potter’s wheel and intricately hand carved. They are made from ^6 Porcelain and are fired in my electric kiln, once to harden the clay and make them safe to handle and a second firing to a much higher temperature to mature the clay body and the applied glaze.
When they are leather hard and after the foot has been trimmed, I either add a layer of color made from the throwing slurry with added Mason Stains, or I choose to work on an all white surface. I first lightly pencil a grid onto the surface to guide my design, then start to build the patterns that the shape seems to want.
The carving process is slow and quiet, and concentration is present as each line is carefully carved in relation to what is beside it and the space around it. A piece may take from 3 to 10 hours for me to complete the decorated surface.
I always use a clear glaze on the interior, and sometimes choose to leave the exterior unglazed. The contrast between the matte and reflective surfaces enliven the visual character of the piece.
The glaze is lead free and food safe. The pots are safe in dishwashers but are not recommended for use in the oven or microwave.